On-Demand Packaging Equipment Service to Support Your Production Needs
On-Demand Packaging Equipment Service to Support Your Production Needs
Blog Article
Expert Product Packaging Devices Solution for Seamless Procedures
In today's hectic manufacturing settings, the relevance of skilled product packaging devices service can not be understated. Such services not only enhance operational efficiency yet also play an important role in decreasing downtime and making certain item high quality. By leveraging experienced technicians for precautionary maintenance and prompt repairs, companies can browse the intricacies of equipment monitoring (packaging equipment service). The landscape of equipment solution is developing, presenting both challenges and opportunities that necessitate further exploration. What variables should companies consider when purchasing these crucial services to protect their competitive edge?
Value of Specialist Solution

Additionally, regular maintenance by professionals aids extend the life-span of product packaging tools. Specialist company are geared up with thorough understanding of numerous equipment types and industry criteria, permitting them to do preventative maintenance successfully. This aggressive technique not just minimizes the probability of unanticipated break downs but additionally enhances general functional reliability.
In addition, expert service can significantly add to conformity with governing requirements. Product packaging devices should adhere to stringent safety and security and high quality guidelines, and specialist specialists make certain that these criteria are fulfilled continually. This not only safeguards product integrity however also protects the business's reputation.
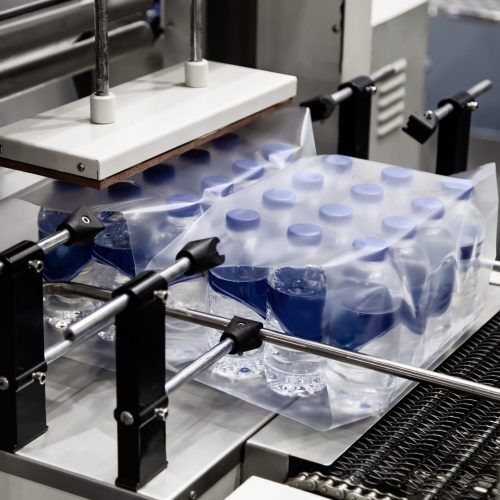
Advantages of Professional Support
Engaging expert support for packaging equipment not only boosts operational efficiency but additionally delivers a series of extra benefits that can substantially affect an organization's profits. Among one of the most remarkable advantages is the reduction of downtime. Specialist service technicians can quickly identify and fix concerns, ensuring that manufacturing lines stay active and reducing the economic losses related to still machinery.
Additionally, specialist support frequently includes preventative maintenance, which can expand the life expectancy of product packaging devices. By consistently servicing equipment, potential problems can be determined and attended to prior to they rise into costly repairs or substitutes. This aggressive method not just conserves money yet additionally enhances product quality by guaranteeing that devices operates within ideal specifications.
In addition, leveraging the knowledge of experienced specialists can cause enhanced conformity with market laws. These experts stay updated on the current standards and can direct services in applying best methods, consequently staying clear of possible legal liabilities.
Types of Packaging Devices Solutions
When it involves product packaging equipment services, services can select from a selection of alternatives customized to fulfill their specific needs. These services generally come under several categories, each designed to enhance operational efficiency and minimize downtime.
Preventive upkeep solutions concentrate on normal evaluations and upkeep jobs to ensure that tools runs smoothly and lowers the likelihood of unexpected failures. This aggressive technique can prolong the life expectancy of additional resources machinery and boost performance.
Repair solutions are important for addressing devices malfunctions or failings - packaging equipment service. Proficient service technicians identify the issues and execute necessary repair work, making sure that the equipment is restored to ideal working problems immediately
Installment solutions are vital when introducing brand-new packaging equipment. Specialists deal with the setup, making certain that the machinery is incorporated correctly right into existing lines and features as meant.
Educating solutions offer personnel with the necessary abilities and expertise to run tools successfully. This training can cover whatever from fundamental operation to sophisticated troubleshooting.
Last but not least, speaking with solutions supply strategic insights right into optimizing product packaging processes, aiding organizations determine areas for improvement and execute finest techniques. Overall, choosing the best mix of these services can considerably boost packaging operations.
Secret Attributes to Search For
What crucial features should services consider when choosing product packaging tools solutions? Furthermore, the accessibility of comprehensive support services, consisting of setup, upkeep, and troubleshooting, guarantees that companies can count on prompt aid when issues occur.
Another key attribute is the adaptability of service offerings. A provider that can adjust to developing business find more demands, such as changes in manufacturing volume or packaging specs, will be crucial in keeping effectiveness. Furthermore, modern technology integration need to be a priority; modern-day packaging tools services must incorporate innovative modern technologies, such as automation and real-time click surveillance, to boost efficiency.
Lastly, credibility and consumer feedback must not be overlooked. Involving with testimonies and study can provide a more clear photo of a company's reliability and high quality. By taking into consideration these important attributes, businesses can make educated choices that will certainly support their product packaging procedures and contribute to general success.
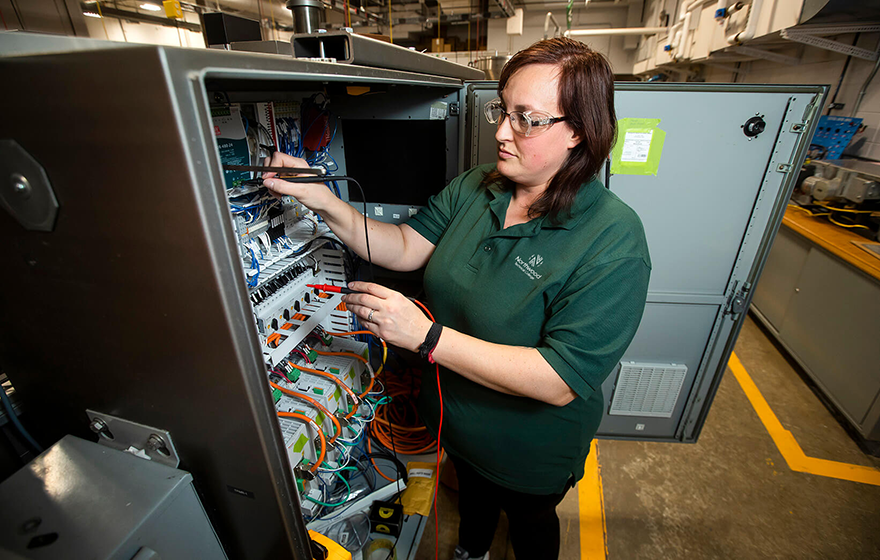
Buying Long-Term Success
Spending in long-term success in packaging tools services needs a critical approach that prioritizes sustainability and scalability. Firms have to concentrate on picking equipment that not just satisfies current functional requirements but also accommodates future development and technological improvements. This insight minimizes interruptions and improves general efficiency.
An essential element of this investment is the normal maintenance and service of equipment. Establishing a proactive service routine lowers downtime and prolongs the life expectancy of equipment, inevitably resulting in cost savings. Partnering with skilled provider guarantees that the tools is enhanced for efficiency, thus keeping high production requirements.
Moreover, integrating ingenious innovations, such as automation and IoT connectivity, can considerably improve operational capabilities. These advancements allow for real-time monitoring and information evaluation, making it possible for business to make educated decisions that align with their long-term objectives.
Last but not least, buying worker training on new technology and ideal methods promotes a culture of continuous renovation. By growing a competent workforce, companies can adjust to altering market demands and keep their one-upmanship. Inevitably, an all natural method that encompasses tools, solution, technology, and labor force advancement positions firms for sustained success in the product packaging industry.
Verdict
In final thought, specialist packaging devices solution plays a crucial role in guaranteeing seamless operations within production settings. By focusing on these services, companies can attain optimum operational efficiency and prolong the life-span of their equipment.
Report this page